Our services
Our Services
VATECH’s team of experts will be dedicated to providing total solutions for all rotating equipment, electrical motor, valve and compressor challenges in oil & gas industry. Our engineers will identify root-cause issues and create innovative solutions through expert engineering. Then, Our Performance Test Specialists will verify optimum performance, and our condition monitoring solution will provide real-time data to keep your equipment working at peak conditions.
Backed by years of our engineers and specialists experience, with a broad range of pump, motor and other equipment types and an unparalleled commitment to our customers, our goal is to achieve lasting solutions to complex technical problems.
With over 20 years of experience of our engineers and specialists in oil & gas sector, we will do it right – the first time.
Technical Evaluation Services
With our highly skilled on-site reliability team, you can rest assured that your pumping systems, motors, valves and other equipment will be in good health. Whether you need on-site troubleshooting for a complex condition or a routine field evaluation of your equipment, VATECH Technical Evaluation Services can provide comprehensive results to improve the performance.
VATECH Technical Evaluation Services provides expert troubleshooting and on-site engineering services for your equipment. Our master equipment improvement engineers will work with your maintenance and engineering staff to provide complete reliability support for your equipment installation base, whether the equipment is recently commissioned or has been in service for many years.
Providing On-Site Solutions for Complex Equipment Problems
VATECH 's highly skilled technical improvement engineers will work with your maintenance and engineering staff to provide complete reliability support for your equipment installation base, whether the equipment is recently commissioned or has been in service for many years.
To help our customers maintain critical equipment running and operating, our technical improvement engineers will review the equipment operating and maintenance history, provide a thorough on-site inspection, and perform various system testing.
VATECH 's Technical Improvement Engineers will provide a multitude of diagnostic services, ranging from minor issues to very complex analysis.
Our Technical team, backed by various global network of cooperating partner service centers, will provide assessments not just on your equipment but the entire system. This testing is provided as either a troubleshooting service or a general health inspection of your equipment.
Quality Equipment Repair
- Our Repair Capabilities
What constitutes a quality equipment repair? Quite simply, VATECH pays attention to the details - a thorough inspection process, extensive process control procedures and stringent acceptance criteria, engineering support and review - all carried out by an experienced work force dedicated to providing a quality service.
- Inspections
Our very thorough and detailed inspection process is the foundation of a quality repair that can prevent recurring problems, extend equipment life and reduce long-term repair costs. During the inspection process we often uncover issues which, if left unattended, could result in premature failure of a component and the equipment.
The inspection of an equipment could include taking over 900 separate readings. Not only do we record various data, but we also take extensive readings and analyze them.
The inspection process and the report of our findings is a great opportunity for our engineers and technicians to work with the customer’s maintenance team to discuss options for not only repairing but for improving the equipment’s performance and reliability.
24/7 Field & Emergency Services
When an equipment is critical to the operation of your plant or facility, it is important to work with an experienced Field Service Team. VATECH’s Field Technicians have extensive cross-OEM knowledge, enabling them to work on many makes and models. Our specialists come from different world-wide manufacturer backgrounds.
Our experience, coupled with our extensive collection of historical data and engineering support, enables us to provide solutions for your equipment problems. Whether it is providing technical support or offering supervision to supplement your maintenance crew during an outage, you can count on VATECH for quality field and turnkey services.
Our Field Services include:
- Installation and start-up
VATECH 's experienced Field Service Technicians are skilled at performing and supporting pump, motor and valve installations and startups.
Whether installing equipment repaired by us or new or replacement components, our cross-OEM trained Field Service Technicians will be your lifeline to a timely project completion and successful equipment start-up.
- Field Machining and repair
VATECH’s Field Service Technicians use state-of-the-art tools and techniques for critical equipment repairs in the field. We employ the use of portable rolling tool carts which contain rigging, micrometer, and storage gang boxes in addition to several hydraulic boring bars of various sizes and other necessary tools.
- Turnkey services
VATECH’s Field Service Technicians will work with your plant liaisons to coordinate and plan the entire job from start to finish. We can provide all the tools and labor to complete the job and can perform the finer details of the work scope.
Communication is the most important part of successful turnkey projects, and VATECH will coordinate daily with your plant liaisons to assure timely updates of emerging issues and job status.
- Project management
VATECH offers technical oversight support which enables a plant to free up personnel during an outage so they can manage peripheral projects.
Our Field Service Technicians work directly with your maintenance staff to supervise all activities onsite that will achieve the requirements of the work scope.
VATECH Field Service Technicians offer guidance to fine tune the work scope and project timeline, discover efficiencies, work with third party labor groups, and determine cost reduction opportunities.
- System Troubleshooting and Field Engineering
VATECH 's experienced Field Service Technicians work closely with plant personnel and our in-house engineering team to solve system related challenges. We understand that problems can be caused by many variables within the system.
Our inter-department collaboration coupled with the availability of collected data resources in our library enable us to thoroughly evaluate your system. A thorough evaluation by advanced field engineering staff can help to determine areas of the system that can be modified or enhanced to meet or exceed performance requirements or cost reduction opportunities.
Emergency Field Response
- Emergency Services
We understand that when an emergency occurs, you need to get your process or plant back up as quickly as possible. As VATECH’s Emergency Response we will strive to be the best in the industry, providing 24/7 support 365 days of the year.
Engineering Services
From its inception, VATECH has maintained a strong focus on engineering as an essential part of the repair process, providing hands-on engineering support in the field and on the shop floor.
As a result, we have pioneered many specialized repair processes, reliability improvements and engineering upgrades. As an independent company, VATECH offers unbiased engineering analysis in each repair situation.
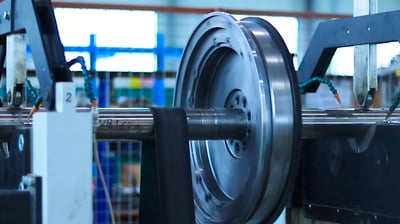
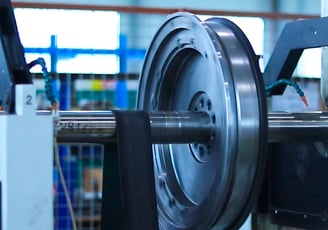
Reverse Engineering
Reverse engineering is the examination, testing and analysis of a component to define and document all of the parameters and critical attributes necessary to manufacture, repair or modify it. Dimensions, tolerances, surface finishes and fit or clearance to adjoining items, are determined. Our process also includes an analysis of the chemical and physical properties of the material of construction as well as its hardness and residual stresses.
Reverse engineering is quite different from "replicating." We are not interested in just replicating the existing component as it is, but also in evaluating the failure modes and defining the critical characteristics required to minimize the possibility of failure in the newly manufactured piece. Engineering knowledge and experience is always an important part of our process.
While accuracy, thoroughness and technology are important elements of reverse engineering, it is VATECH’s equipment specific engineering knowledge, understanding and experience that distinguish and define our process.
Root Cause Analysis
To identify root causes of equipment problems, we will combine our very thorough and detailed inspection process with an evaluation of a equipment's field operating conditions and maintenance history. This more in-depth approach can prevent costly forced outages by revealing latent conditions that may be causing repeated failures.
Our engineering team has the knowledge and experience to analyze the existing problems and to recommend a quality solution based on sound engineering analysis and proven practices.
Engineering Studies
While many problems can be identified during a physical inspection of the equipment when it is removed from service during either a planned or unplanned outage or turnaround, other more complex problems may require an extensive analysis of the equipment and its system.
We have the experience and resources to perform such engineering studies or to participate as part of a consulting engineering team to analyze complex equipment and system problems.
Engineered Upgrades
VATECH strives to diversify an in-depth equipment knowledge that we believe is unique in our industry. While OEM’s traditionally focused on repairing their own equipment, we from the outset have developed a knowledge base that includes experience across a broad spectrum of manufacturers and equipment designs.
We understand that as an independent company, we need a unique capability of understanding the different designs and materials employed by various OEM’s as well as their successes or failures in specific applications and operating environments. Based on this data, VATECH is in an excellent position to improve OEM designs for their intended service.
Our Engineered Parts Solutions
VATECH’s engineering experience, use of the latest design technologies, and quality manufacturing processes enable us to support emergency parts requirements and provide component repeatability with a high degree of accuracy. When you require a spare part or component and are facing a long lead time, we can meet your needs in a reduced time frame. We’re on it.
Our Parts Solutions supports all customers in manufacturing difficult-to-source parts, such as impellers, diffusers, discharge heads, casings, bowls, suction bells, and much more. VATECH Parts Solutions can fulfill manufacturing needs for customers without long wait times, compromised quality, and high costs.
As the need for spare parts became a need for finished, high-quality products, many advanced tools were added to the shop as well our affiliate partners in the region. Utilizing state-of-the-art technology such as 3D printing and design, VATECH Parts Solutions aims to establish itself as a center that possessed sophisticated casting and manufacturing capabilities with a delivery time that beat OEMs by weeks – if not months.
Complete Architecture Services
From concept to completion, our architecture services use the latest technology and techniques to deliver exceptional results.
Lifestyle-Enhancing Design
Our architecture services take into consideration your lifestyle and preferences to create spaces that are both beautiful and functional.
Collaborative Design Services
We work collaboratively with our clients throughout the design process to ensure their vision is realized in the final product.